August 1994 Bulletin
Compressive Stress Depth
Print this Newsletter
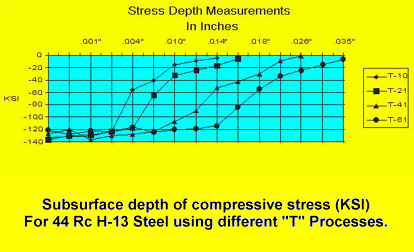
Click
Here
to see Coupon Lambda X-Ray Diffraction Curves Taken in June 1997
Tensile residual stresses are a factor on used tooling running production die cast parts as well as on NEW tooling that only has been sampled for production. After a NEW tool receives its final tempering, there still remains tensile stresses on the surface of the steel. These stresses, if left untreated, can cause premature initiation of thermal heat checking. It is important for a
die caster to be aware of this condition so that the necessary corrective action can be taken to counteract it. Inducing a uniform depth of residual compressive stress on a die's surface is a critical step to extending the life of the tool, especially in the case of EDM production methods.
Cracks originate at the surface of a die and propagate from the outside into the surface. A uniform compressive stress layer on the tool's surface will not allow the propagation of a crack into or through this compressive layer unless the effective yield strength of the steel is exceeded. This is a fact of metallurgical engineering and is the principle upon which MetaLL ifeÒ is based. In this test we measured, by using X-ray diffraction using PROTO portable measuring equipment,
the depth and degree of compressive stress for each of our "T" processes.
For our test specimen we used one of our sample Viscount (Rockwell 44c) bars. This bar is identical to the one that many of our customers and potential users already have in their possession. The bar has four processes applied to it. By using a calibrated digital system of measuring with X-rays, the average depth of compression was measured starting at the surface and then again at sequential
depths for each of the processed areas. Presently, the only way of measuring the relative depth of compressive stress is by destructive means. The destructive method that was finally chosen required the removal of surface material to obtain stress values at the numerous subsequent varying depths. Electro-polishing was used to remove the Viscount material. This method of removal does not upset or
cause a change in the stress KSI at the newly exposed steel depth and therefore allows accurate readings at these depths. The resulting KSI number shows relative stress values with compression indicated by a "-" whereas tension would be indicated by a "+". Each reading taken was at the same physical location on the bar's surface.
The above graph, shows a chart plotted from each group of readings for each
processed area. As confirmed by this test, the amount and depth of compressive
stress at different subsurface levels was found to be directly proportional to
the "T" numbers, with the T-10 process having the least amount and T-61 having
the most. The T-61 also showed the greatest sustained amount of compressive
stress with magnitudes that exceeded -50KSI at .018" of an inch below the
surface. Both the T-41 and T-61 provide an optimum compressive stress value
along with depth of penetration for maximum protection from thermal stress
related heat checking and currently are the most popular of the processes. With
the exception of T-10, which is only used on small core pins or in zinc
applications, all processes showed approximately the same compressive levels at
about .004" of an inch in subsurface depth. The T-21 process, still provides
adequate levels of compressive stress and can easily be utilized in applications
where any increase in topography is prohibitive or the configuration of the die does not allow an aggressive type of surface compressive. For larger tools, such as
transmission or barbecue dies, we also now offer a T-71 process for a greater degree of topography and compressive stress protection.
In October we were featured on the Discovery Channel in a show called "Business Today - "Manufacturing Technologies, the Future and Beyond". Copies of this program are available on VHS video tape by contacting us.
|